Simon Wanstall
Prosthetic limbs have improved significantly within recent years, moving on from wooden legs and mechanical hooks to running blades and robotic hands. However, some of the main drawbacks of modern functional prosthetics are that they are still made from hard materials with stiff mechanical parts and limited sensing capabilities. The solution to these problems could be found in the field of soft robotics. With recent advances in this area, like flexible sensors and soft actuators, the functional prosthetics of the future could look and feel a lot closer to their biological counterparts.
The aim of this project is to develop the technologies within soft robotic prosthetic devices through research and experimentation, ideally resulting in the construction of a novel soft robotic prosthetic arm. This aim will be met by conducting multiple research projects, covering three main areas of the soft robotics field:
- Manufacturing
- Human-Robot Interaction
- Manipulation and Control Techniques
Manufacturing is a challenge for soft robotics research because traditional processes for making soft components, like injection moulding with metal dies, are time-consuming and expensive. Digital manufacturing techniques, like 3D printing, are being utilised to overcome these issues. However, more research is needed to improve digital manufacturing techniques to create parts that match the capabilities of alternatives made of hard materials. The first goal of this project is to innovate in the area of 3D printing, through iterative testing of soft robotic fingers manufactured using novel digital processes. Other experiments in this area could include the development of soft sensors in e-skins, or experimenting with biomimicry in the design of semi-flexible bone-like structural parts.
In the case of soft robotic prosthetics, human-robot interaction research mainly covers safety, comfort, and ease of use. Safety and comfort go hand-in-hand because uncomfortable prostheses often injure users and, without heavy countermeasures, can also cause injury to people around them. Also, for a prosthetic to be easy to use, it should be light, comfortable and highly functional. These challenges could be overcome by soft robotic prostheses, being safer and more comfortable due to their compliance, while also reducing the need for heavy safety systems. Relevant experiments covered by this project could include designing an attachment cuff that can adapt to daily bodily changes and increase comfort, and developing new structural geometries of prostheses to reduce weight.
Finally, manipulation and control techniques for soft robots can be difficult to devise due to the compliance of soft components. However, overcoming this issue could allow soft robotic prostheses to become the new standard, due to potential advantages in other areas. Experiments in this area could include, the development of soft actuators inspired by the mechanics of human muscles, and the application of e-skin sensors to control the grip strength of the prosthesis.
Education:
I initially attended schools in County Durham, England for my primary and secondary education. These were Edmondsley Primary School and The Hermitage Academy. I then attended the Sixth Form program within The Hermitage Academy to obtain my A-Level qualifications, which include a C grade in Mathematics, a C in Physics, and a B in Art and Graphic Design. I was then awarded a place on the Mechanical Engineering undergraduate course at Heriot-Watt University in Edinburgh. At University, I was involved in many interesting projects including, devising a way to provide underprivileged people in Nairobi with internet access, designing an innovative test device for a Royal Navy supplier, and researching mechanical methods to combat bacterial biofilms by studying insect wings. I left University with a First Class Honours Degree and, a year later, was accepted onto this PhD course at the Edinburgh Centre for Robotics.
Research Interests:
My research interests are based around soft robotics, prostheses, medical devices, biomimicry, biomechanics, materials science, and digital manufacturing techniques.
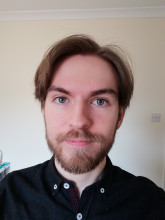